bottom and top unheading device
Manufacturer: Delta Valve
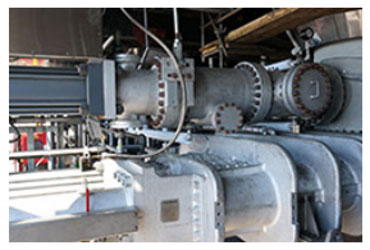
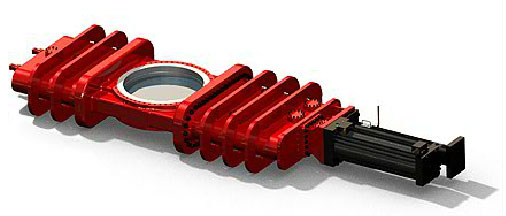
DeltaValve is a world leader in the manufacture of bottom and top valves for coke drums with long experience and proven technology in the field.
DeltaValve Bottom and Top Coke Drum Decoking Devices are the lightest and most compact fully automated equipment in the industry. The small space occupied by these devices makes them ideal both for remodeled installations with space limitations and for new constructions.
O Decoking Device consists of a sliding gate valve specially designed for application and is available with the traditional hydraulic drive or with the electric drive system threaded with planetary rollers (PRS), an exclusive product from DeltaValve.
The system is designed for fully automated, safe and reliable operation and can be used in intermittent or batch applications. This technology has made remote decoking operation a reality.
O DeltaValve Decoking Device incorporates a single drawer. This simple design reduces potential failures, minimizing downtime and maximizing production.
The DeltaValve Coke Drum Top Decoking Device mounts directly to the drum to create a permanent connection at the top flange. Just like the bottom device, the top device uses patented dynamic seat technology that is watertight, robust and reliable.
Delta Valve has the largest installed base in refineries in the world with proven technology and has already supplied all Petrobras refineries such as: REVAP, REPAR, RPBC, REPLAN and others.
FLUXO is the representative and distributor of DeltaValve in Brazil, has a local base and structure for after-sales support, technical assistance and supply of spare parts.
Additional equipment of the delayed coking unit
CenterFeed™ injection device
DeltaValve's innovative CenterFeed™ injection device is designed to resolve issues of uneven thermal distribution and severe thermal transients experienced when using side load configurations. CenterFeed accomplishes this by simply returning charge streams to the center of the coke drum, which results in more consistent operation throughout the process, steam range and cooling cycles, which together contributes to lower stresses and longer service life. of the drum. CenterFeed can be configured with electric, electro-hydraulic or hydraulic drive, and can also be integrated into any safety interlock system.
The benefits of recreating the centralized flow pattern are:
- Establishes a straight upward flow pattern in the center of the drum;
- Allows the formation of channels in the center of the coke drum during the cycle;
- Dramatically reduces circumferential temperature variations recorded at the side feed inlet;
- Reduces severe stresses on the drum wall caused by circumferential variations in drum temperature, resulting in longer service life and a reduction in drum damage such as cracking, rippling and banana effect.
Main products:
- DeltaValve offers a full range of delayed coking products, including:
- Decoking devices for bottom and top of sliding drawer type coke drums
- CenterFeed™ injection devices
- Automatic switching drilling/cutting tools
- Protective devices for cutting tools
- After-sales, spare parts and field services
- Engineering and installation services
Certifications:
- ASME and BPVC decoking devices, Section VIII Div. I and II
- ASME B31.3 Center Load Devices
- DeltaValve maintains the following stamps and design certifications:
- AS ME
- Stamp “U”, Division I
- “R” stamp
- National Council Register
- Pressure Equipment Directive
- (PED) (2014/68/EU)
Related articles:
- Delta Valve celebrates 20th anniversary of slide valve technology
- DeltaValve and FLUXO organize a base for coke plant valve aftermarket
- First maintenance on DeltaValve coke drum valves in Brazil
- DeltaValve: hegemony in coke units