A desalter, with globally recognized technology, will be manufactured in Brazil to improve operational efficiency in refineries
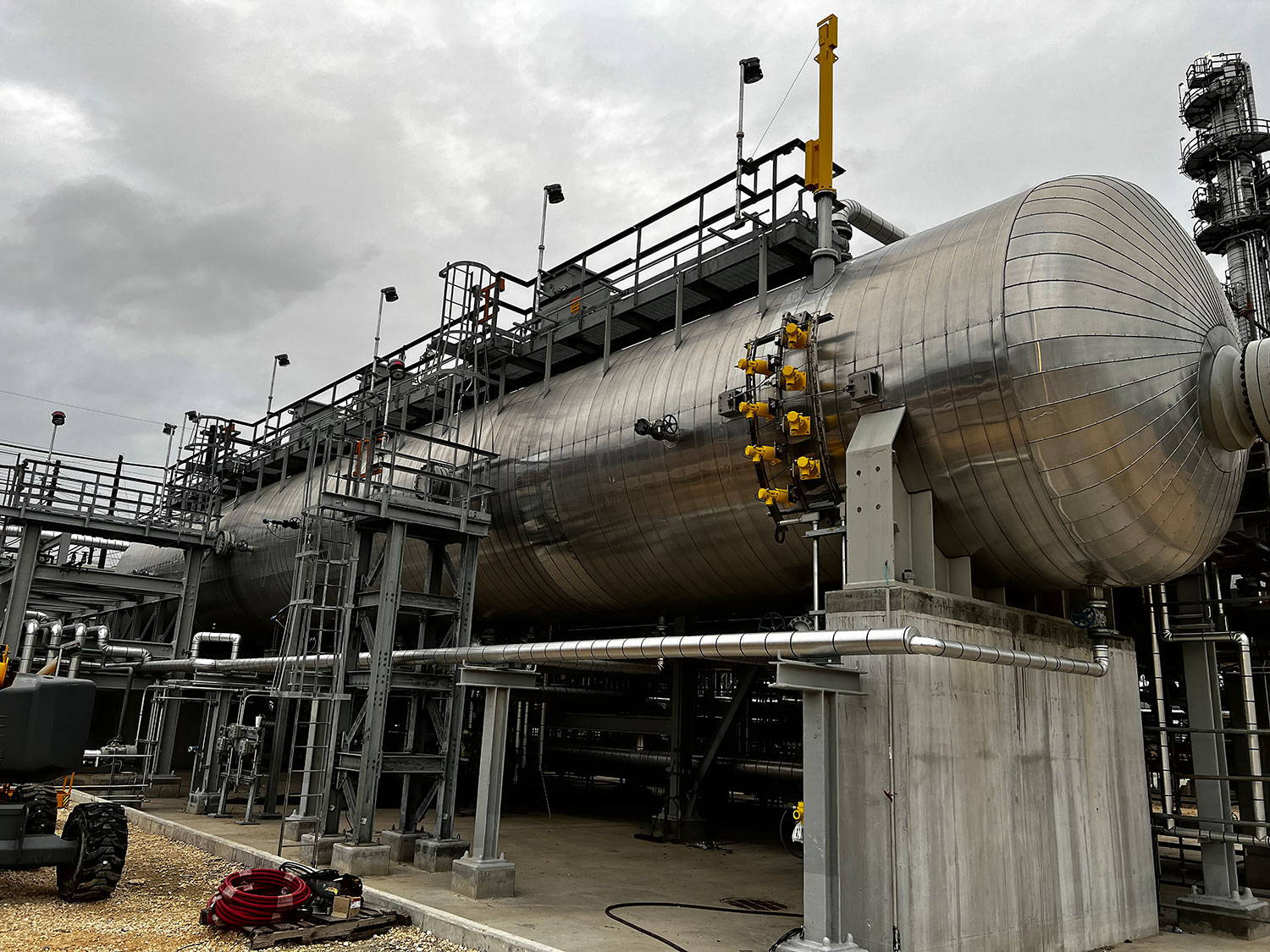
Desalting is an essential process in the refining industry, responsible for the efficient removal of water, mineral salts and other contaminants present in oil. This critical step prevents corrosion and equipment clogging, ensuring the integrity of the facilities, the quality of the derivatives and the continuity of operations. The adoption of advanced technologies at this stage plays a fundamental role in optimizing refining, promoting process stability and ensuring that the oil meets the required standards.
High efficiency technology applied in the Refinery
President Bernardes (RPBC) of Petrobras
Petrobras' Presidente Bernardes Refinery (RPBC), located in Cubatão (SP), took an important step towards modernizing its plant by starting the installation of a new horizontal flow desalter, to be used as the first stage of the desalting process.
With a capacity to process up to 6,000 m³/day, the equipment will provide greater flexibility, allowing the processing of oil with API density 30.5° and improving its quality. The solution will enable RPBC to achieve a level of treated oil with less than 0.5% of basic sediments and water (BS&W), a high standard. In addition, with the second stage of the process, the equipment has an efficiency of over 99% in salt removal.
A significant highlight of this project is the manufacturing of the equipment in Brazil, carried out by FLUXO, in partnership with NEET PROCESS of Texas (USA). The desalter vessel will be manufactured in ASTM 516-Gr 70 steel and FLUXO will also be responsible for the field assembly, commissioning, start-up and testing of the equipment, in addition to after-sales technical support. NEET PROCESS, in turn, will provide the proprietary internals, as well as basic and detailed engineering. This collaboration between the two companies will allow RPBC to have access to a cutting-edge solution, with advanced technology and local manufacturing, reducing costs and ensuring operational efficiency.
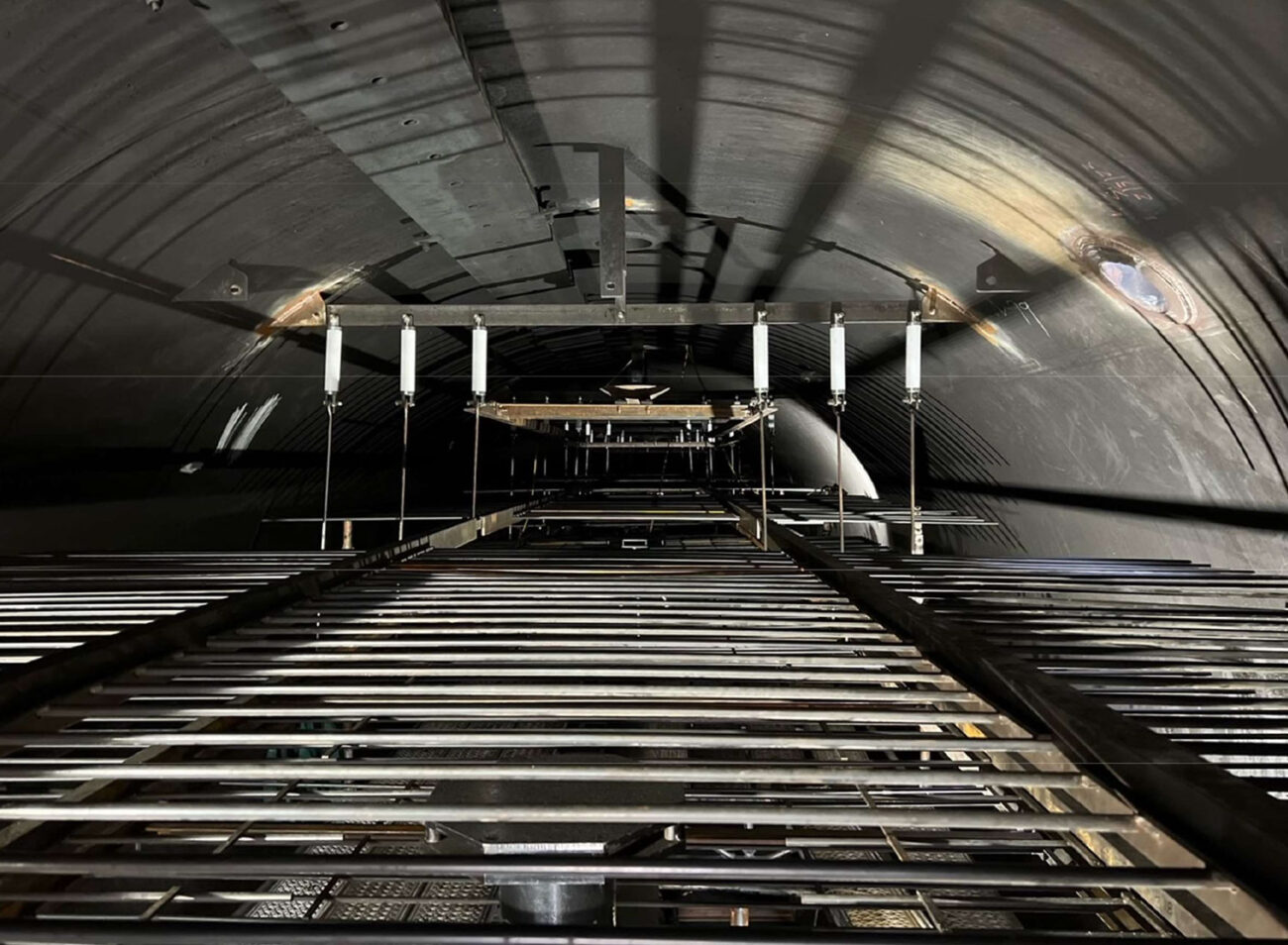
Main specifications:
- Type: Horizontal flow desalter
- Capacity: 6,000 m³/day
- Applied voltage: 14,000 volts
- Salt removal efficiency: >99%
- Dimensions: Ø 3.657mm x 9.770mm (length)
- Total weight: 43 tons
- National manufacturer: FLOW
- Engineering/internals: NEET PROCESS (USA)
How the desalter works
The desalter is an electrostatic treater that uses high voltage to separate water, salt and other contaminants from oil. The process begins with the addition of wash water (10%) to the crude oil, forming an emulsion. This mixture is conveyed to the interior of a pressure vessel, where it is subjected to an electric field of 14,000 volts, generated by three 50 kVA transformers each (alternating current). The electrostatic field created induces the coalescence of the brine droplets, that is, the smaller droplets attract each other and form larger droplets and, due to the difference in density, the oil and water are separated.
The separation process is extremely fast, occurring in seconds. The treated product is then drained out of the upper part of the vessel, while the brine and other contaminants are removed from the lower part of the vessel.
The installation of this new desalter at RPBC will represent an improvement in the quality of the oil at this refinery. In addition to expanding processing capacity with greater operational flexibility, the project boosts local engineering and strengthens the national capital goods industry, reducing foreign dependence. For the market, this is a milestone in the modernization of the refining park, with a direct impact on the efficiency, safety and competitiveness of the oil and gas chain.