OPLA expands in Paulínia with FLUXO Advanced Technologies
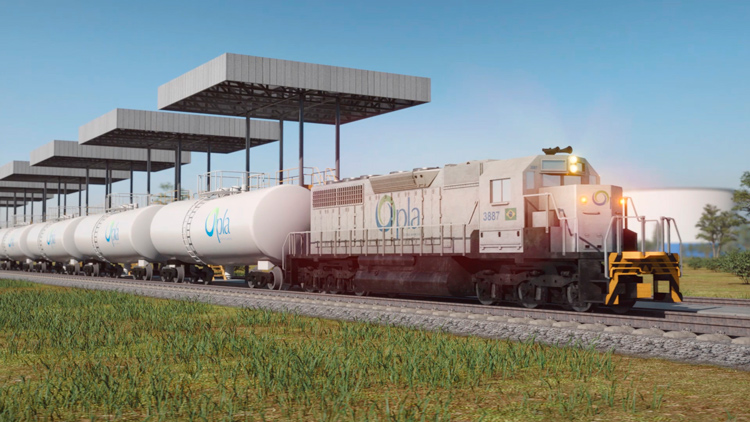
OPLA, a joint venture between BP and Ultracargo, has announced the expansion of its terminal in Paulínia, highlighting the implementation of innovative technologies from FLUXO Soluções Integradas. The initiative aims to further strengthen its position in the market, operating, in addition to ethanol, diesel jet fuel and, in the future, gasoline.
Specializing in fiscal measurement systems and systems for treating volatile organic compounds (VOCs), FLUXO was chosen to implement a new vapour recovery unit (URV) and advanced systems for loading and unloading fuel by rail.
OPLA manages one of the most significant fuel terminals in Paulínia-SP. This terminal, known for its substantial storage capacity and operational efficiency, represents a vital link in the fuel distribution chain in Brazil.
Opla was inaugurated in 2017 and today has the largest independent ethanol terminal in Brazil, with a tankage capacity of 180,000 m3. The structure is multi-modal and has a pipeline and access to railroads connected to the center-west and north of Brazil. It is also strategically located to serve São Paulo, as well as being accessible by road to the Porto de Santos, where Ultracargo currently operates its largest terminal in terms of storage capacity.
Vapor Recovery Unit Technology
FLUXO Soluções Integradas, under a license agreement with world leader Jordan Technologies (a Cimarron group company), is bringing an advanced Vapour Recovery Unit (URV) to the OPLA terminal. This unit is a significant innovation in the field of environmental engineering, standing out mainly for the inclusion of the HORI vacuum pump, a crucial component for its efficient performance.
The core technology of FLUXO's vapor recovery unit employs an adsorption/absorption system using activated carbon. This method is the most effective in capturing volatile organic vapors (VOCs) present in the gases emitted during fuel transfer operations. Activated carbon, with its surface area, adsorbs the vapors, efficiently removing them from the air. This process not only purifies the air, but also allows for the recovery of adsorbed fuel, maximizing efficiency and minimizing waste.
A crucial aspect of this technology is the regeneration of the activated carbon, which is where the HORI vacuum pump plays a vital role. This pump removes the VOCs from the activated carbon bed by means of a vacuum applied to the system. These vapors are then condensed through an absorption tower and returned to the fuel storage process. The HORI pump, which is exclusive to FLUXO/Jordan, represents a technological innovation for URVs that have been in use in Brazil and worldwide for 10 years. It is an oscillating vane vacuum pump with a carbon seal, without the need for an oil or glycol seal, and free from impurity blockages due to its design.
FLUXO is the leading supplier of Vapour Recovery Units in Brazil, with 100% of the units supplied approved in accordance with the efficiency requirements of the Brazilian environmental agencies.
Rail Loading and Unloading Skids
A key aspect of the expansion of OPLA's terminal in Paulínia is the implementation of advanced automated rail fuel loading and unloading systems, supplied by FLUXO. These systems are crucial to guaranteeing efficiency, precision and safety in the terminal's operations.
Rail Loading Skids
For diesel loading, FLUXO will supply 7 rail loading skids. Each of these skids is equipped with Faure Herman helical turbine flow meters, recognized worldwide for their accuracy and reliability for a wide range of density and viscosity variations. These meters are essential for ensuring accurate flow measurement during loading, providing efficient and precise operation.
Rail Unloading Skids
For rail unloading, FLUXO will implement 3 double skids with high embedded technology. These skids use Yokogawa's coriolis flow meters, which, in addition to measuring mass and volumetric flow, also measure fuel density in real time. This functionality allows for continuous and precise monitoring, ensuring that the fuel received complies with the required specifications. Furthermore, the system has an automatic interlock mechanism, which is activated in the event of deviations, thus ensuring greater safety and quality control during the unloading process.
The automation of the loading and unloading skids will be controlled by the modern preset Fusion4, from Honeywell Enraf partner. The equipment will be responsible for safety interlocks, batch control, volume correction at 20 C, and totalization of loaded and unloaded products. Also noteworthy is the use of OCV digital control valves and EXATA grounding and overflow monitors.
The flow meters and presets used in the loading and unloading skids have the INMETRO Model Approval Ordinance, as well as the complete design, ensuring their compliance with national fiscal measurement and custody transfer standards. This certification is a key element, as it validates the accuracy and reliability of the systems implemented, reinforcing the integrity and transparency of fuel transfer operations. The system will undergo initial verification procedures by IPEM, legitimizing the skids for operation in accordance with legal requirements.
The expansion of OPLA's terminal in Paulínia, with the partnership established with FLUXO, represents an important step in Brazil's fuel sector.
In addition to facilitating the flow of corn ethanol production, the terminal's interconnection with railroads that reach the Midwest will promote more efficient means of taking other liquid bulk to the interior of Brazil, contributing to the development of regions with infrastructure and supply deficits.
The implementation of the Vapor Recovery Unit (URV) and advanced railway loading and unloading systems reflects Opla's commitment, through BP and Ultracargo, to technological innovation, operational efficiency and environmental responsibility.
"By integrating our advanced Vapour Recovery Unit and the rail loading and unloading systems, we are not only expanding the terminal's operational capacity, but also setting new standards in efficiency and environmental sustainability. It's a clear demonstration of how technology, when applied innovatively, can generate significant economic benefits while protecting the environment." - Fábio André Alves, Commercial Director of FLUXO.
This project is an example of how strategic collaboration and the application of advanced technologies can result in cleaner, more efficient and cost-effective operations, benefiting both industry and the environment.